Current Location:Home > NEWS > Industry news
NEWS

Ceramic heaters for semiconductor equipment components
类别:Industry news 发布时间:2025-02-26 11:41:49 浏览:58 次
In the front-end process (FEOL) of semiconductor manufacturing, various process treatments need to be carried out on the wafer, especially heating it to a certain temperature, and there are strict requirements because the uniformity of temperature has a very important impact on product yield; At the same time, semiconductor equipment also needs to operate in environments with vacuum, plasma, and chemical gases, which requires the use of ceramic heaters. Ceramic heater is an important component of semiconductor thin film deposition equipment, applied in the process chamber, directly in contact with the wafer, carrying and enabling the wafer to obtain stable and uniform process temperature, and conducting high-precision reactions on the wafer surface to generate thin films.
The thin film deposition equipment for ceramic heater applications generally uses ceramic materials mainly composed of aluminum nitride (AlN) due to the high temperature involved. Because aluminum nitride has electrical insulation and excellent thermal conductivity; In addition, its thermal expansion coefficient is close to that of silicon and it has excellent plasma resistance, making it very suitable for use as a component in semiconductor equipment.
The electrostatic chuck (ESC) is mainly used in etching equipment, with aluminum oxide (Al2O3) as the main material. Due to the fact that the electrostatic chuck itself also contains a heater, taking dry etching as an example, it is necessary to control the wafer at a specific temperature within the range of -70 ℃ to 100 ℃ to maintain certain etching characteristics. Therefore, the wafer temperature needs to be precisely controlled by heating or dissipating heat through the electrostatic chuck. In order to ensure the uniform heat distribution on the wafer surface, electrostatic chucks often need to increase the temperature control zones and separately control the temperature of each zone to improve the process yield. Of course, with the development of technology, the distinction between traditional ceramic heaters and electrostatic chucks has become blurred, and some ceramic heaters have dual functions of high-temperature heating and electrostatic adsorption.
Basic structure of heater
The ceramic heater includes a ceramic base that carries the wafer, and a cylindrical support body on the back that provides support for it. Inside or on the surface of the ceramic base, in addition to the resistance element (heating layer) used for heating, there are also radio frequency electrodes (radio frequency layer). In order to achieve rapid heating and cooling, the thickness of the ceramic base should be thin, but being too thin can also lead to a decrease in rigidity. The support body of the heater is generally made of a material with a thermal expansion coefficient similar to that of the base, so the support body is often made of aluminum nitride material. The heater adopts a unique structure of shaft joint at the bottom, which can protect the terminals and wires from the influence of plasma and corrosive chemical gases. There are heat conduction gas inlet and outlet pipelines in the support body to ensure uniform temperature of the heater. Chemical bonding is performed between the base and the support using a bonding layer.
Inside the heater base, a resistance heating element is embedded. It is formed by screen printing using conductive paste (tungsten, molybdenum, or tantalum) to create vortex shaped or concentric circular circuit patterns. Of course, metal wires, metal mesh, metal foil, etc. can also be used. When using screen printing, prepare two ceramic plates of the same shape and apply conductive paste on one of their surfaces. Then, it is sintered to form a resistance heating element, and the other ceramic plate is sandwiched between the resistance heating element and overlapped to produce a resistance element embedded in the base.
Basic performance of heater
When using plasma enhanced chemical vapor deposition (PECVD) equipment to prepare thin films, the main factors affecting film uniformity and thickness are plasma characteristics and process temperature. Firstly, the density and distribution of plasma directly affect the uniformity and deposition rate of the thin film. A uniformly distributed plasma can ensure that the active gas fully reacts on the substrate surface, thereby forming a uniform thin film. The uniform distribution of plasma is closely related to the RF mesh embedded in the heater. Secondly, specific process temperatures ensure excellent thermal uniformity. Ceramic heaters ensure that the surface temperature of the wafer fluctuates within ± 1.0%. For example, the temperature fluctuation of heaters produced by NGK insulator in Japan is less than 0.1%, which is an excellent indicator.
When manufacturing ceramic heaters, there are also requirements for the purity of aluminum nitride materials. Slight changes in composition may alter the color and electrical properties of the heater under certain conditions, and of course, the plasma coupled with it may also change its characteristics. In addition, the density, thermal conductivity, and bulk resistivity of aluminum nitride materials can all affect the performance of heaters.
According to literature, the bulk resistivity of a heater at 500 ℃ needs to be at least within the range of 5.0E+9 to 1.0E+10 Ω· cm, and the bulk resistivity at 600 ℃ to 700 ℃ needs to be at least within the range of 1.0E+8 to 1.0E+9 Ω· cm. The bulk resistivity of a typical aluminum nitride ceramic heater often drops rapidly from 500 ℃, leading to leakage phenomena.
According to market research reports, the global market size of aluminum nitride ceramic heaters for semiconductors is expected to reach 33 million US dollars in 2022, and is projected to reach 78.529 million US dollars by 2031, with a compound annual growth rate of 10% during the forecast period. Manufacturers of aluminum nitride ceramic heaters for semiconductors mainly include NGK insulator, MiCo Ceramics, Boboo Hi Tech, AMAT, Sumitomo Electric, CoorsTek, Semixicon LLC. In 2023, the top five global manufacturers will hold approximately 91.0% of the market share. In terms of product types, currently 8 inches are the most important segmented product, accounting for approximately 45.9% of the market share. In terms of product applications, chemical vapor deposition equipment is currently the main source of demand, accounting for approximately 73.7% of the market share.
Article source: ICPMS Cold Knowledge gz07apple
Disclaimer: The content of this article is for sharing only and the copyright belongs to the original author. We would like to express our gratitude to the original author. If there are any copyright issues, please contact us for deletion! thank you!
Chinese distributor of Japanese light metal aluminum hydroxide, alumina, and granulation materials
Exclusive distributor of French ALTEO alumina granulation material in China
Chinese distributor of Korean KC alumina and aluminum hydroxide
INMATEC Ceramic Feed China Seller from Germany
Indian HINDALCO alumina Chinese distributor
European MAL alumina distributor in China
Chinese distributor of auxiliary materials for industries such as imported ceramics, polishing, and thermal conductivity
Address: Room 601, 6th Floor, Shuozhi Building, Minghu Road, Fengze District, Quanzhou City, Fujian Province
Phone (tel): 0595-22170091
Website: www.choloon-trade.com
www.changfar-tech.com
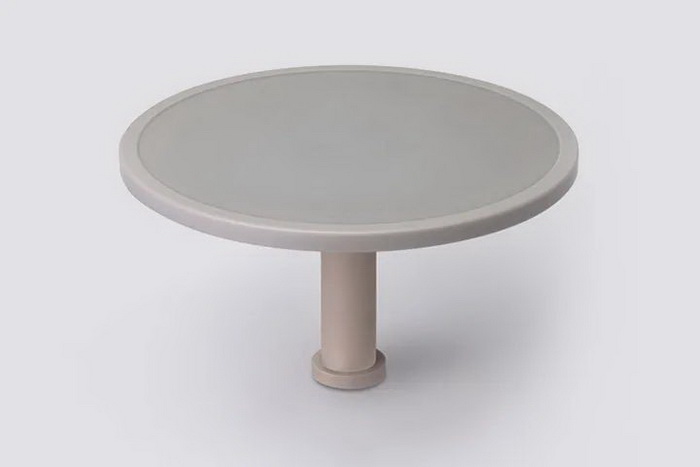
The thin film deposition equipment for ceramic heater applications generally uses ceramic materials mainly composed of aluminum nitride (AlN) due to the high temperature involved. Because aluminum nitride has electrical insulation and excellent thermal conductivity; In addition, its thermal expansion coefficient is close to that of silicon and it has excellent plasma resistance, making it very suitable for use as a component in semiconductor equipment.
The electrostatic chuck (ESC) is mainly used in etching equipment, with aluminum oxide (Al2O3) as the main material. Due to the fact that the electrostatic chuck itself also contains a heater, taking dry etching as an example, it is necessary to control the wafer at a specific temperature within the range of -70 ℃ to 100 ℃ to maintain certain etching characteristics. Therefore, the wafer temperature needs to be precisely controlled by heating or dissipating heat through the electrostatic chuck. In order to ensure the uniform heat distribution on the wafer surface, electrostatic chucks often need to increase the temperature control zones and separately control the temperature of each zone to improve the process yield. Of course, with the development of technology, the distinction between traditional ceramic heaters and electrostatic chucks has become blurred, and some ceramic heaters have dual functions of high-temperature heating and electrostatic adsorption.
Basic structure of heater
The ceramic heater includes a ceramic base that carries the wafer, and a cylindrical support body on the back that provides support for it. Inside or on the surface of the ceramic base, in addition to the resistance element (heating layer) used for heating, there are also radio frequency electrodes (radio frequency layer). In order to achieve rapid heating and cooling, the thickness of the ceramic base should be thin, but being too thin can also lead to a decrease in rigidity. The support body of the heater is generally made of a material with a thermal expansion coefficient similar to that of the base, so the support body is often made of aluminum nitride material. The heater adopts a unique structure of shaft joint at the bottom, which can protect the terminals and wires from the influence of plasma and corrosive chemical gases. There are heat conduction gas inlet and outlet pipelines in the support body to ensure uniform temperature of the heater. Chemical bonding is performed between the base and the support using a bonding layer.
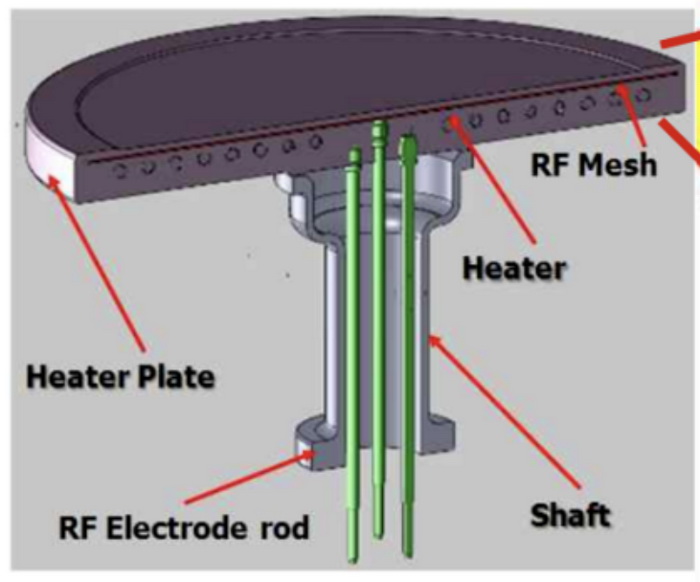
Inside the heater base, a resistance heating element is embedded. It is formed by screen printing using conductive paste (tungsten, molybdenum, or tantalum) to create vortex shaped or concentric circular circuit patterns. Of course, metal wires, metal mesh, metal foil, etc. can also be used. When using screen printing, prepare two ceramic plates of the same shape and apply conductive paste on one of their surfaces. Then, it is sintered to form a resistance heating element, and the other ceramic plate is sandwiched between the resistance heating element and overlapped to produce a resistance element embedded in the base.
Basic performance of heater
When using plasma enhanced chemical vapor deposition (PECVD) equipment to prepare thin films, the main factors affecting film uniformity and thickness are plasma characteristics and process temperature. Firstly, the density and distribution of plasma directly affect the uniformity and deposition rate of the thin film. A uniformly distributed plasma can ensure that the active gas fully reacts on the substrate surface, thereby forming a uniform thin film. The uniform distribution of plasma is closely related to the RF mesh embedded in the heater. Secondly, specific process temperatures ensure excellent thermal uniformity. Ceramic heaters ensure that the surface temperature of the wafer fluctuates within ± 1.0%. For example, the temperature fluctuation of heaters produced by NGK insulator in Japan is less than 0.1%, which is an excellent indicator.
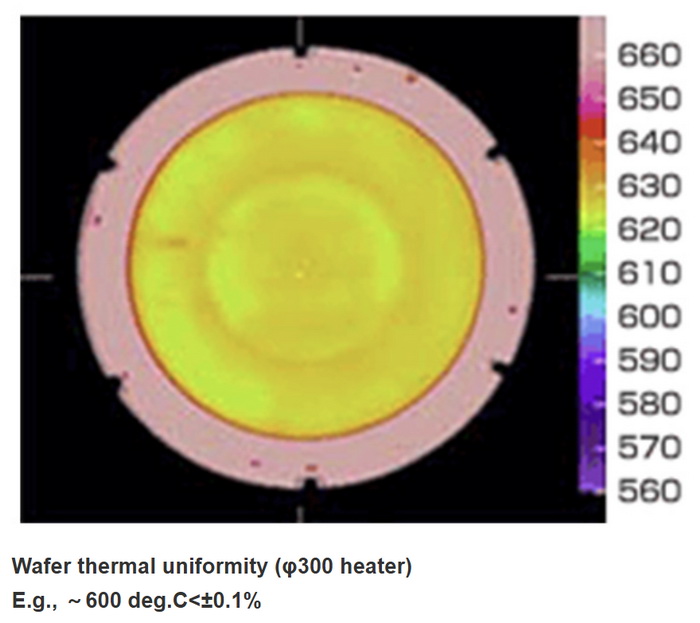
When manufacturing ceramic heaters, there are also requirements for the purity of aluminum nitride materials. Slight changes in composition may alter the color and electrical properties of the heater under certain conditions, and of course, the plasma coupled with it may also change its characteristics. In addition, the density, thermal conductivity, and bulk resistivity of aluminum nitride materials can all affect the performance of heaters.
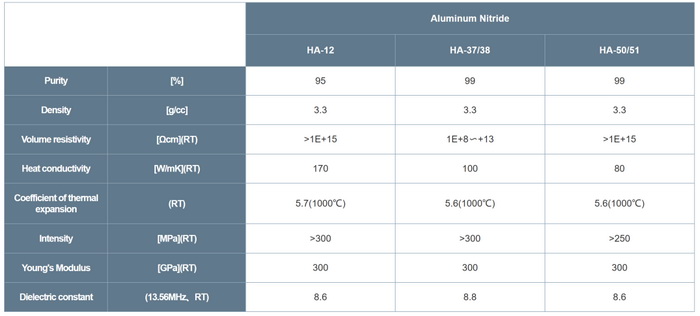
According to literature, the bulk resistivity of a heater at 500 ℃ needs to be at least within the range of 5.0E+9 to 1.0E+10 Ω· cm, and the bulk resistivity at 600 ℃ to 700 ℃ needs to be at least within the range of 1.0E+8 to 1.0E+9 Ω· cm. The bulk resistivity of a typical aluminum nitride ceramic heater often drops rapidly from 500 ℃, leading to leakage phenomena.
According to market research reports, the global market size of aluminum nitride ceramic heaters for semiconductors is expected to reach 33 million US dollars in 2022, and is projected to reach 78.529 million US dollars by 2031, with a compound annual growth rate of 10% during the forecast period. Manufacturers of aluminum nitride ceramic heaters for semiconductors mainly include NGK insulator, MiCo Ceramics, Boboo Hi Tech, AMAT, Sumitomo Electric, CoorsTek, Semixicon LLC. In 2023, the top five global manufacturers will hold approximately 91.0% of the market share. In terms of product types, currently 8 inches are the most important segmented product, accounting for approximately 45.9% of the market share. In terms of product applications, chemical vapor deposition equipment is currently the main source of demand, accounting for approximately 73.7% of the market share.
Article source: ICPMS Cold Knowledge gz07apple
Disclaimer: The content of this article is for sharing only and the copyright belongs to the original author. We would like to express our gratitude to the original author. If there are any copyright issues, please contact us for deletion! thank you!
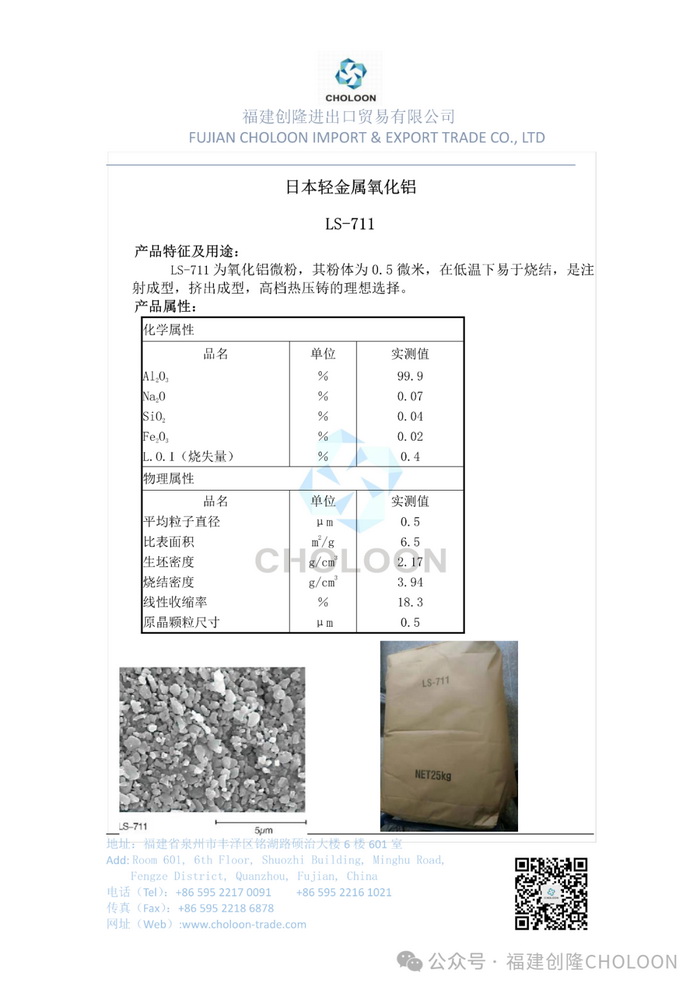
Chinese distributor of Japanese light metal aluminum hydroxide, alumina, and granulation materials
Exclusive distributor of French ALTEO alumina granulation material in China
Chinese distributor of Korean KC alumina and aluminum hydroxide
INMATEC Ceramic Feed China Seller from Germany
Indian HINDALCO alumina Chinese distributor
European MAL alumina distributor in China
Chinese distributor of auxiliary materials for industries such as imported ceramics, polishing, and thermal conductivity
Address: Room 601, 6th Floor, Shuozhi Building, Minghu Road, Fengze District, Quanzhou City, Fujian Province
Phone (tel): 0595-22170091
Website: www.choloon-trade.com
www.changfar-tech.com